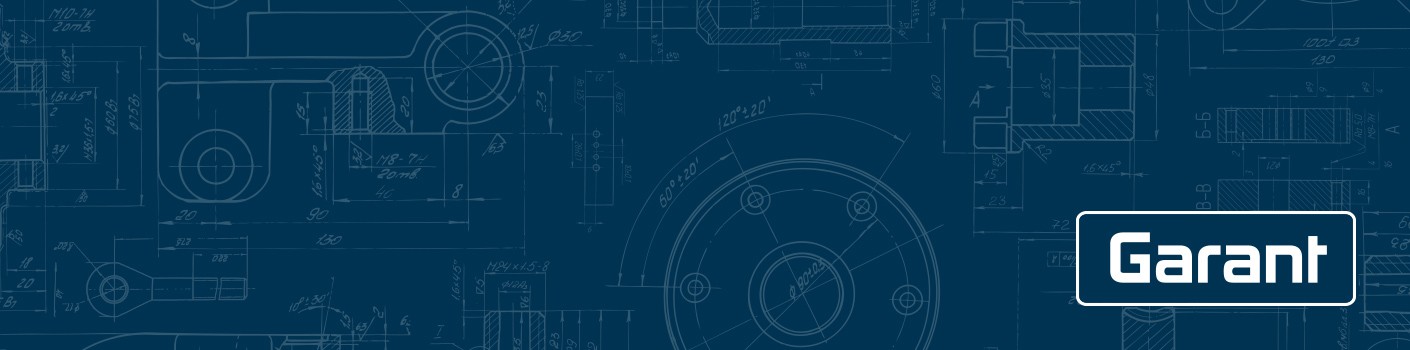
New milling cutter generation for aluminium machining
High-performance milling cutter GARANT Master Alu – offers absolute process reliability and is reassuringly efficient

The latest generation of milling cutter GARANT Master Alu impresses with its particularly high performance in machining aluminium. The innovative high-performance milling cutters are characterised by long service life, and achieve extreme feed rates and cutting speeds. Highest surface qualities can be achieved in a short space of time, thus achieving extraordinarily high efficiency in machining.
The extensive product line GARANT Master Alu provides the ideal solution for every machining task, be it finishing, roughing, plunging (drilling) or ramping. Furthermore, the HPC tools are available uncoated or with the latest DLC coating (also with geometry for plunging). The colour of the coating is based on the ISO code colour, enabling all employees to identify the application field of the milling cutter quickly and easily.
More and more aluminium is being processed in industrial production. Its special characteristics make it very valuable.
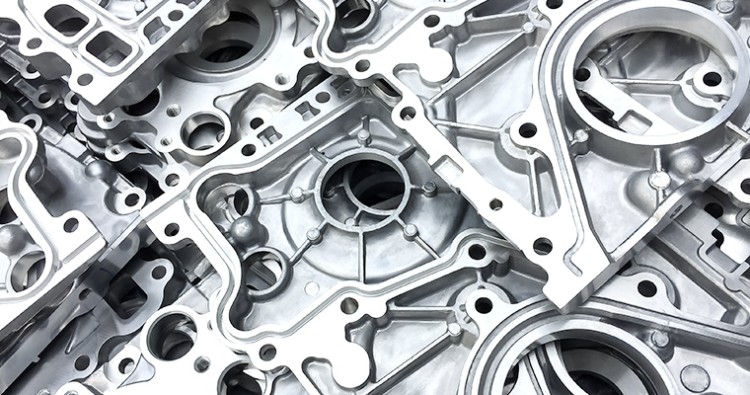
More and more aluminium is being processed in industrial production. Its special characteristics make it very valuable.
- Aluminium is lightweight: Weight reduction is a critical advantage for energy saving, especially in the automotive and aerospace industries.
- Aluminium is stable: The use of alloys achieves strengths virtually the same as in steel.
- Aluminium is corrosion-resistant: A thin oxide layer quickly forms and protects the metal.
- Aluminium is easily processed: Complicated hollow sections and geometries are achievable by extrusion.
- Aluminium is a good conductor: The high thermal conductivity, in conjunction with the high specific heat capacity tend to favour the good machinability and permit high cutting speeds.
- Conservation of resources: Aluminium lends itself very well to recycling.
Get to know all GARANT Master Alu milling cutters:
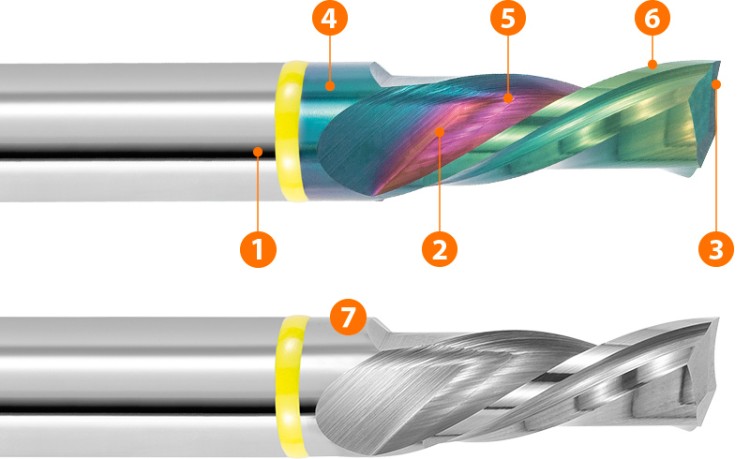
GARANT Master Alu solid carbide milling cutter, precision balanced
The tool geometry is designed especially for grooving and contour milling. The GARANT Master Alu solid carbide milling cutter is available uncoated or with the latest generation DLC coating in green (in line with the ISO code).
Note: The milling cutters have a special ground finish to counteract the unbalance. This ensures the best possible balancing quality of G1.8 and also achieves the best possible balancing quality at high speeds for each diameter.
- Substrate with the best tensile strength.
- Special flute profiles; chips are immediately evacuated away. Polished flutes for quick and reliable chip evacuation.
- Tool geometry for grooving and contour milling.
- The latest generation of DLC coating in green (in line with ISO-Code).
- Strengthened core diameter for very high stability.
- Selective cutting edge preparation for very high process reliability. Formation of built-up edges is thus prevented as much as possible.
- GARANT Master Alu solid carbide milling cutter, precision balanced, also available uncoated.
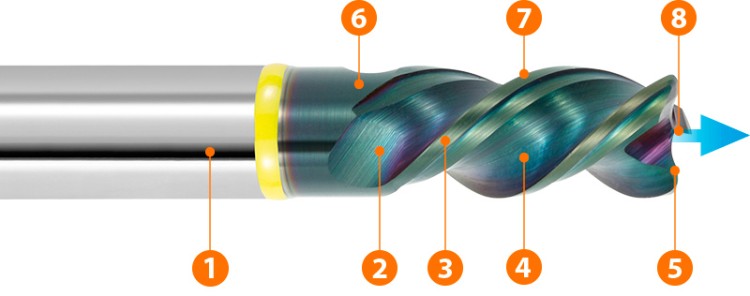
GARANT Master Alu PickPocket
Especially suitable for plunging (drilling) and ramping. The innovative end face geometry permits highest feed rates and avoids build-up of chips when drilling. The GARANT Master Alu PickPocket is available in five different versions: uncoated or with the latest generation of DLC coating in green (in line with the ISO code), with and without internal cooling, with short or long shank for working at greater depths. It therefore offers an ideal solution for every processing task.
Recommendation: At maximum feed rates, wet machining is preferred in order to prevent an adhesion of the machining material, which can occur at high temperature.
- Substrate with the best tensile strength.
- Reinforced core diameter for very high stability when milling slots.
- Variable helical pitch for smooth running in all applications. For the best possible surface quality.
- Polished flutes for quick and reliable chip evacuation. Specially designed with large flutes for non-ferrous materials. For quick and reliable evacuation of high volumes of chips.
- Innovative end face geometry for plunging (drilling) and ramping at very high feed rates. Avoids build-up of chips when drilling..
- The latest generation of DLC coating in green.
- Selective cutting edge preparation for very high process reliability. Formation of built-up edges is thus prevented as much as possible.
- Version with internal cooling ideal for direct plunging (drilling) and ramping. The innovative end face geometry permits highest feed rates and avoids build-up of chips when drilling
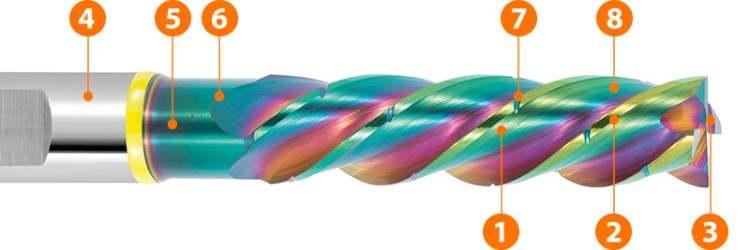
GARANT Master Alu TPC milling cutter
With chip separators for controlled chip breaking.
Recommendation: Due to the high heat generation during TPC milling in non-ferrous metals, the use of wet machining is preferable. The formation of built-up edges in particular is thus counteracted as much as possible. In turn, the cutting data ae can be increased.
1. Defined cutting edge preparation to ensure process reliability and very high surface qualities.
2. Variable helical pitch to prevent vibration and promote a homogeneous cutting action.
3. Face geometry recessed on the inside for reliable helix milling and plunging.
4. Solid carbide grade with outstanding bending strength, designed for machining non-ferrous materials.
5. Latest generation of DLC coating in green.
6. Reinforced core diameter for stability and optimised force distribution during TPC milling operation.
7. Chip separator design and arrangement for extra-short chips to avoid chip nest formation.
8. Optimised flutes specially for TPC machining of aluminium to prevent chip jams and for ideal chip evacuation.
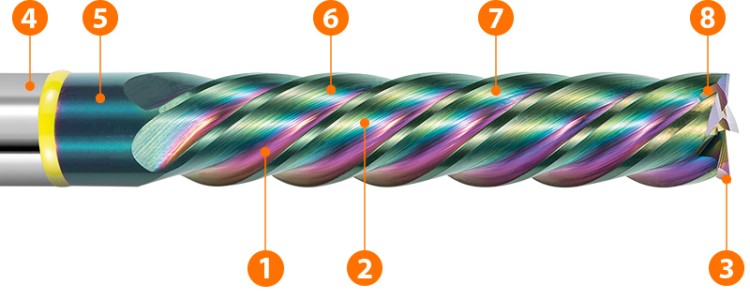
GARANT Master Alu solid carbide finishing cutter
The GARANT Master Alu finishing cutter with 5 cutting edges is particularly effective for finishing operations. Its edge preparation is designed especially for the main application of machining aluminium, making it much sharper than tools designed for machining steel. Comparison of the honed cutting edges: GARANT Master Alu solid carbide finishing cutter r= 3,599 µm vs. GARANT Master Steel solid carbide finishing cutter r= 9,721 µm.
The milling cutter is available in three lengths – all have the latest generation of DLC coating in green (in line with the ISO-Code).
- Strengthened core diameter for very high stability.
- Variable helical pitch for smooth running and for the avoidance of vibration.
- Five cutting edges for effective finishing operations.
- Substrate with the best tensile strength.
- The latest generation of DLC coating in green.
- Polished flutes to avoid material adhesions.
- Specially designed with deep flutes for non-ferrous materials. For quick and reliable evacuation of chips and to avoid chips jamming.
- Selective cutting edge preparation for very high process reliability. Reduction or prevention of vibration for very high surface quality.
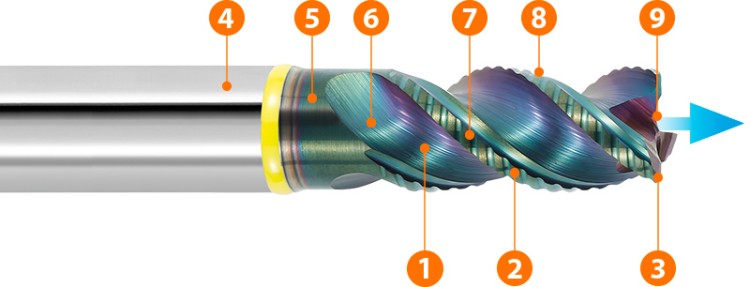
GARANT Master Alu SlotMachine
Especially suited to plunging (drilling) and ramping. The innovative end face geometry permits highest feed rates and avoids build-up of chips when drilling. The GARANT Master Alu SlotMachine is available in three different versions: with or without internal cooling, with short or long cutting edge. All versions have the latest generation of DLC coating in green (in line with the ISO-Code).
Application recommendation: At maximum feed rates, wet machining is preferred in order to prevent an adhesion of the machining material, which can occur at high temperature!
- Polished flutes for quick and reliable chip evacuation. Specially designed with large flutes for non-ferrous materials. For quick and reliable evacuation of high volumes of chips.
- Knuckle form profile for small chips and soft cutting. The depth of the knuckle form profile is designed to produce chips that are as short as possible, even at high feed rates.
- Innovative end face geometry for plunging (drilling) and ramping at very high feed rates. Avoids build-up of chips when drilling.
- Substrate with the best tensile strength.
- The latest generation of DLC coating in green.
- Reinforced core diameter for very high stability when milling slots.
- Selective cutting edge preparation for very high process reliability. Formation of built-up edges is thus prevented as much as possible.
- Variable helical pitch for smooth running in all applications.
- Version with through-coolant is ideal for direct plunging (drilling) and ramping.