Gauge Block Deep Dive
A Guide to Proper Usage and Care
In the realm of precision measurement, one tool stands out for its unparalleled accuracy and versatility - gauge blocks. These seemingly simple, yet highly precise blocks play a crucial role in various industries where accuracy is paramount. Having a good gauge block set in your workshop can go a long way in terms of your project’s accuracy.
What are gauge blocks used for?
Gauge blocks, also known as gage blocks, slip gauges, or Jo blocks, are standardized blocks of metal or ceramic used for precision measurement. Typically rectangular in shape, these blocks come in sets of varying lengths, allowing for the combination of different blocks to achieve specific measurement dimensions. The primary purpose of gauge blocks is to set up or calibrate measurement devices like micrometers, calipers, and height gauges with utmost precision.
Industries such as manufacturing, aerospace, automotive, and engineering heavily rely on gauge blocks for tasks like calibration, quality control, and dimensional inspection. Their versatility and accuracy make them indispensable for ensuring the quality and precision of machined components and products.
What are the different grades of gauge blocks?
The different grades of gauge blocks correspond to a specific level of accuracy. The most common grades are as follows:
Grade 0: Highest grade accuracy working gauge block. Also known as laboratory grade.
Grade 1: Medium grade accuracy working gauge block. Also known as inspection grade.
Grade 2: Lowest grade accuracy working gauge block. Also known as workshop grade.
Wringing your gauge blocks
Wringing is the technique of joining gauge blocks together using the molecular attraction between them. When two gauge blocks are placed together, a wringing action occurs, creating a temporary bond between the blocks. This ensures that the blocks behave as a single, solid unit, maintaining accuracy during measurement tasks.
To achieve a proper wring, ensure that the surfaces of the gauge blocks are clean and free from any contaminants. Lightly oiling the blocks can enhance the wringing process. Gently slide the blocks together and, with a slight twist, separate them. The blocks should now be securely joined, forming a wrung pair ready for precise measurements.
Best post-care practices to get the most of your gauge blocks
Proper care and maintenance are crucial in maximizing the lifespan and accuracy of your gauge blocks. Here are some post-care tips to keep your gauge block set in optimal condition:
Cleanliness is Key: Always clean your gauge blocks after each use. Use a lint-free cloth or tissue along with a mild cleaning solution to remove any dirt, oil, or contaminants.
Storage Matters: Store your gauge blocks in a protective case or cabinet to prevent damage and maintain their accuracy. Avoid exposing them to extreme temperatures or humidity.
Regular Calibration: Depending on the application, grade, and how often they’re being used, gauge blocks will need to be calibrated from every few months to every few years.
Handle with Care: Treat gauge blocks gently to avoid damage to their precision surfaces. Use clean gloves when handling them to prevent fingerprints and oils from affecting measurements.
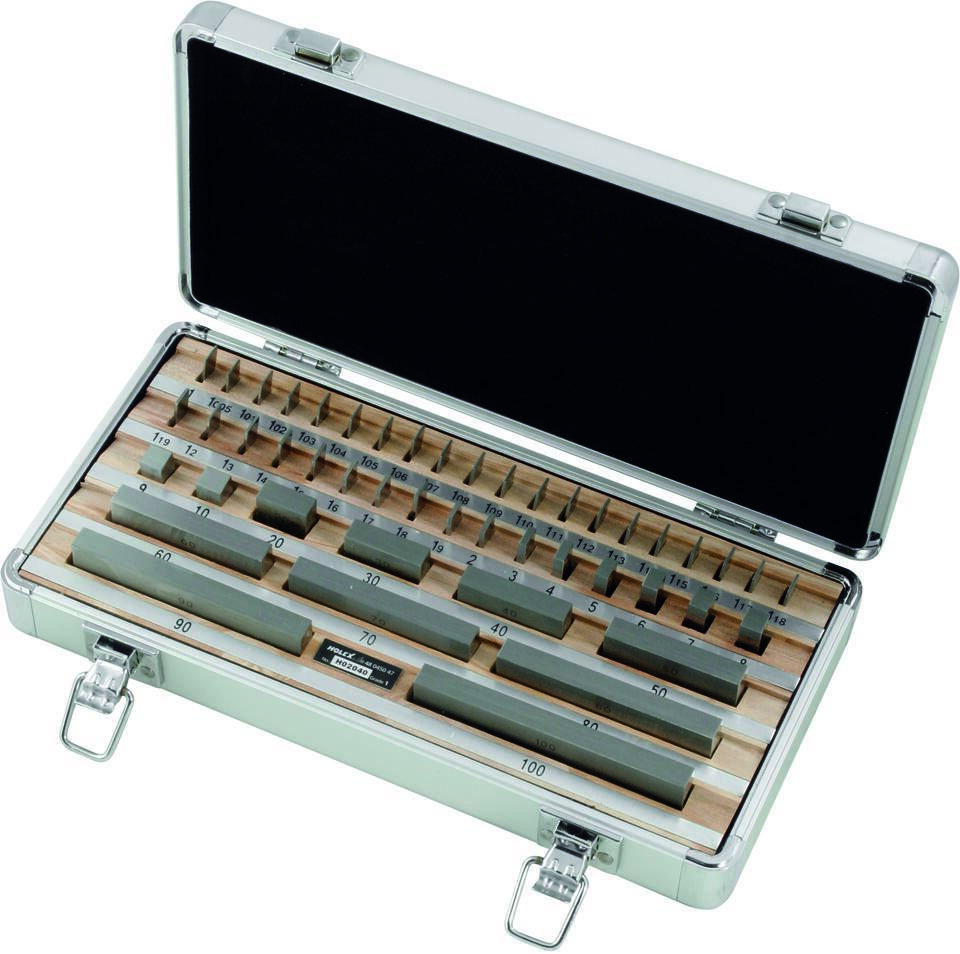
As technology advances, the timeless reliability of gauge blocks remains a cornerstone in precision measurement. Understanding their uses, different grades, the art of wringing, and implementing proper post-care procedures will ensure that your gauge blocks continue to deliver precise measurements for years to come.
Need a gauge block set of your own? Check out our HOLEX Grade 1 workshop quality gauge block set!

Contact Us
Would you like to be advised or ordered by our experts?
We look forward to your call.
> Get in Touch